I love prototypes. Getting a chance to see concepts for the next great thing which for one reason or another never materialized is infinitely interesting to me. On this site, I showed you a prototype Kodak TLR that had one of the most ambitious feature sets I’ve ever seen and a 35mm version of the Kodak Medalist in the Kodak Prototypes of the 1930s article, some really cool Voigtländer prototypes such as an updated Superb TLR and an all new 6×6 SLR which never made it past the design stage, and a very cool SLR concept called the Konica Domirex that had a very unique fixed reflex mirror design.
In this week’s Keppler’s Vault, we go back 40 years to the February 1980 issue of Modern Photography where Herbert Keppler gives us a glimpse of not a prototype camera, but a prototype 35mm film that Kodak was working on likely as a replacement for their venerable 35mm film.
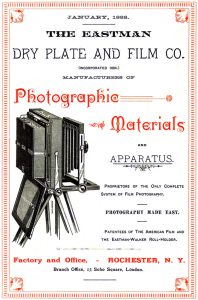
From their earliest days as the Eastman Dry Plate Company, Kodak was always a “film first” company. Sure, they made a lot of different cameras over the years, but with only a few exceptions, most Kodak branded cameras were created to get more people to buy Kodak film.
Kodak was very successful with many of their film formats. The film that would become known as 120 roll film has been in continuous production since 1901 when it was first introduced for their No.2 Brownie box camera. Type 135 double perforated 35mm film first made it’s debut in 1934 for the Kodak Retina and is also still produced. Even some of Kodak’s now discontinued films, such as 116, 122, and 127 were each produced for well over half a century.
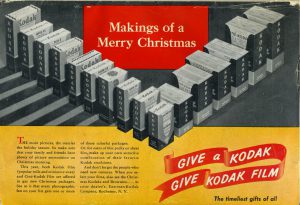
Although many of Kodak’s most popular formats were produced by other competitors like Fuji, GAF, and Ferrania, Kodak had a habit of releasing a new film format with the intent of cornering a new market segment. They did this multiple times with 616 and 620 in 1932, 828 in 1935, Instamatic 126 in 1963, Pocket Instamatic 110 in 1972, Kodak Disc film in 1982, and finally with APS “Advantix” film in 1996.
While each of these films offered some benefit over the films they were intended to replace, they were mostly attempts by Kodak to capture a larger share of the market.
In the late 1970s, a man named Evan Albert Edwards while working for Eastman Kodak, patented a new format of film that could have one day replaced type 135 film. It made sense,as Type 135 film wasted a lot of vertical space on two rows of perforations which were originally created for cinema films and had no real use in a still photographic film. In addition, another 6 to 9 inches of photographic film was wasted on the leader of the film, and often caused amateurs to fumble about when loading.
In the article, Herbert Keppler previews some sketches taken from the patent drawings, along with some insight into the proposed changes in the new prototype film. What’s interesting to me is how many of the new features were eventually incorporated into existing 35mm film without having to completely start over with a new film format.
The following table shows some of the benefits of the new film along with how regular 35mm evolved to incorporate the same feature.
New Prototype Film | Changes to existing 35mm film |
---|---|
A gasketed rectangle showing the film name and type that can be read through a window in the door of the camera. | The idea of an inspection window on the back of a camera to see what kind of film was loaded already existed in the Fuji ST-901 which debuted in 1974, and it worked fine with 35mm film already on the market. By the mid 1980s, this feature would eventually make it into every 35mm camera made by every company. |
Plastic notches in the cassette that the camera can use to “feel” what type of film, ASA speed, or number of exposures it has. | Kodak would introduce the DX encoding system in March 1983 which allowed for this same functionality on existing 35mm cassettes. |
An opaque plastic leader that wraps around the film not in use which not only protects it from light and eliminates the need for the felt light trap on regular 35mm cassettes, but also eliminates the need for film makers to waste photographic film as the leader. | Cameras with fully automatic film loading would soon be introduced which greatly simplified film loading, causing less film, but otherwise no other changes were made to existing 35mm to eliminate wasted film on the leader. |
A hole on the end of the plastic leader which is used to positively attach it to a take up spool, simplifying film loading. | Similar to above. No real changes to 35mm film were needed as by the early 1980s, cameras with automatic film loading hit the market, dramatically simplifying the process of loading film, negating the need for any modifications to the film. |
Notches on the film ends which signal the end of the film, causing the camera to automatically rewind the film likely using some kind of motor. | Later cameras were able to detect the end of a roll of film by measuring resistance on the film. Some cameras like the Nikon N55, used Keppler’s reverse loading idea in which upon installing a new roll of film, the entire unexposed roll is pulled out onto the take up spool, and after each exposure is rewound back into the cassette one exposure at a time. |
Prefogged borders for the exposed image (similar to 126 and 110 film formats) that eliminate unwanted cropping by labs during printing. | 35mm film never used any kind of prefogged film borders which were not only unnecessary as cameras with motorized film transports got much better at advancing the film, but also these borders decrease the exposed image size, reducing quality. |
Single perforations (holes) in the film at each exposure, allowing the camera to positively locate each frame. | 35mm film still uses a double roll of perforations which are still unnecessary. |
Inner cassette spool with gear teeth on both ends, allowing camera makers to rewind the film from either side. | No changes to the physical dimensions of the cassette have ever required dual drive gears in the cassette. |
This new prototype Kodak 35mm film, which is not mentioned by any fancy name, is detailed in the original two page article above, but I was interested enough to do some more digging in an attempt to find the original patent documentation that Keppler refers to.
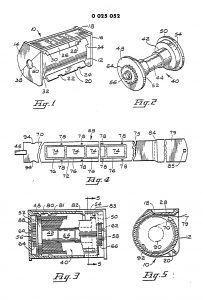
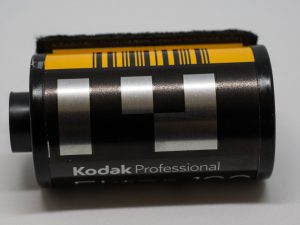
After searching through Google Patents, I was able to locate European Patent EP0025052 which was filed on March 13, 1980 by Evan Albert Edwards a month after the article appeared. Understanding patent law is not something I am good at, but from what I gather, this patent is based off a US patent from March 1979 which I could not locate.
The detailed description on pages 2 – 4 explain the same features covered in the Keppler article along with these illustrations on page 7 which closely resemble Keppler’s drawings.
I kept digging, trying to find an equivalent US patent, but the closest I could find was US4295713, filed on April 9, 1980, also by Evan Albert Edwards. Filed nearly a month apart, the drawings and descriptions in the patents are similar but not identical. Only the European patent shows the thicker opaque leader attached to the film, whereas in the US patent, the leader appears to be made out of the same material as the photographic film and not as wide.
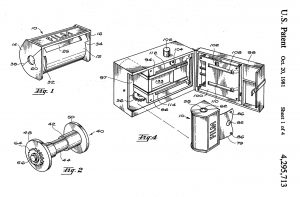
What’s most interesting to me about the US patent is that it references a design patent from Edwards dated March 14, 1979 which suggests he had been working on this film for at least a year.
An even later patent, US4488796 filed on April 25, 1983 by Edwards shows a similar cassette design, but using a style of film with a paper backing similar to Instamatic film, which suggests it might have been a replacement for that format.
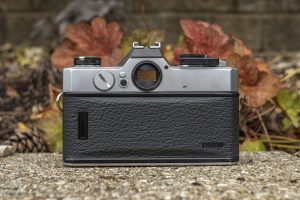
I couldn’t find much information about Evan Albert Edwards other than a variety of other patents issued in his name while working for Kodak from the 1960s to the 1980s. My guess is he was some type of designer they used to come up with proof of concept ideas for future projects, many of which never made it into production.
Today, we have the benefit of hindsight to know that this film was never produced, and it’s probably a good thing too as it likely would have been a miserable failure since it would have been completely incompatible with existing 35mm cameras.
We also know with the failure of APS film that photographers do not like smaller images and this new prototype film would have produced slightly smaller exposed images due to the prefogged frames.
In addition, unlike other times when Kodak released a new format, they were actively making new cameras allowing them to release a new camera along with their new film and in 1980 when this article was published, Kodak had completely gotten out of the 35mm camera market, and the only cameras they had in production were their Instant film cameras and a couple cheap Pocket Instamatic models.
Here we are today in 2020, and the original type 135 film is still being produced, outliving multiple attempts to improve and replace it and I’m no so sure that’s a bad thing!
All scans used with permission by Marc Bergman, 2020.
The vastly improved Kodak 35mm film format of the late 1970s looks a bit like a strip of Kodak 828 Bantam film rolled up onto a Univex 200 film spool from a Univex Mercury (both from the 1930s). I guess good ideas never die, even if they didn’t succeed the first time around. :)=
Yeah, it was pretty much a disaster to begin with, but a fascinating glimpse into the minds at Kodak of the time. I think what Kodak did with APS film was pretty good as most of the changes were good, but the thing that killed it (besides digital) was the smaller exposed image size. Had they kept the size the same, or even increased it, but kept all other APS features, I think it would have been more successful.
Oscar Barnack, and his design “allies” at Canon, would not have been happy if this design had ever superseded standard 35mm: The lack of a proper leader would have made bottom-loading cameras an impossibility. (Today I curse the bean-counters who’ve trimmed modern-day 35mm leaders down to about 1-1/2″, as I have to cut my own 5″ leaders out of the first frame in order to load a vintage Canon RF!)